Common Mistakes in Pallet Distribution – How to Avoid Them
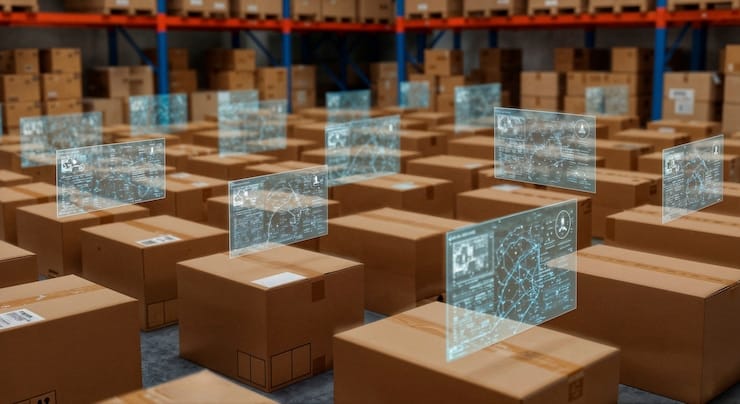
In a supply chain driven by speed, accuracy, and consistency, pallet distribution forms the bedrock of efficient logistics. Businesses across the UK rely on pallet networks to move goods safely and on time—but many still fall into preventable traps that increase costs, cause damage, and reduce customer satisfaction.
Whether you're shipping across town or across the country, partnering with a trusted pallet distribution company can make all the difference. In this post, we’ll dive into the most common mistakes businesses make in pallet logistics and how to avoid them using best practices from Palletline UK, expert pallet racking installation, and optimized palletline logistics systems.
1. Poorly Secured Loads
The Mistake:
Failing to properly secure items on pallets leads to damaged goods during transit, safety hazards, and added costs.
Avoid It By:
-
Using high-quality shrink wrap or stretch film.
-
Evenly distributing weight across the pallet.
-
Employing corner boards and strapping for extra stability.
-
Following industry standards outlined by your pallet distribution company.
Secure loads are essential, especially when operating within a rapid-response network like Palletline UK, where every second and centimeter counts.
2. Overloading Pallets or Racks
The Mistake:
Loading beyond capacity can cause pallet collapse, injury, or rack failure.
Avoid It By:
-
Knowing the maximum load limits of both pallets and racks.
-
Posting visible signage in the warehouse.
-
Hiring professionals for correct pallet racking installation.
-
Conducting routine load checks.
Overloading not only increases the risk of accidents but also slows down operations and leads to product waste.
3. Inadequate Staff Training
The Mistake:
Improper handling by staff who lack training in pallet logistics can result in damages and downtime.
Avoid It By:
-
Offering comprehensive onboarding and ongoing education.
-
Training in forklift operation, pallet stacking, and warehouse navigation.
-
Simulating emergency scenarios for preparedness.
Your team should be fully equipped to navigate the fast-moving pace of palletline logistics environments.
4. Incorrect Pallet Racking Installation
The Mistake:
Poor rack installation can lead to misalignment, safety hazards, and underutilized storage space.
Avoid It By:
-
Hiring certified installation experts.
-
Choosing racking based on SKU size, weight, and turnover rate.
-
Inspecting installations regularly for signs of fatigue or damage.
Proper pallet racking installation not only ensures safety but also enhances overall warehouse efficiency.
5. Inefficient Warehouse Layout
The Mistake:
A disorganized layout creates bottlenecks, delays, and higher labor costs.
Avoid It By:
-
Designing the layout based on item velocity (fast-moving items near dispatch zones).
-
Ensuring clear aisle paths for forklifts and pallet trucks.
-
Using vertical space with optimized racking systems.
Partnering with a pallet distribution company can bring expert insight into high-performance warehouse designs.
6. Skipping Maintenance and Inspection
The Mistake:
Failure to inspect pallets, racks, and handling equipment can lead to unexpected breakdowns.
Avoid It By:
-
Establishing routine inspection schedules.
-
Replacing damaged pallets and repairing racking immediately.
-
Logging issues digitally to track trends over time.
In high-output networks like Palletline UK, system reliability is non-negotiable.
7. Using Low-Quality or Inconsistent Pallets
The Mistake:
Cheap or mismatched pallets cause loading inefficiencies and shipping damage.
Avoid It By:
-
Standardizing pallet sizes and materials.
-
Working with a reputable pallet distribution company that ensures pallet quality.
-
Inspecting pallets before reuse.
A consistent pallet base enhances stacking efficiency and ensures compatibility with automation systems.
8. Lack of Real-Time Tracking
The Mistake:
Blind spots in tracking lead to lost shipments and delayed responses to transit issues.
Avoid It By:
-
Integrating RFID, GPS, or barcode tracking into your TMS.
-
Using platforms that offer live shipment updates.
-
Collaborating with providers that specialize in palletline logistics with real-time visibility.
Data is power. Real-time tracking enables proactive decision-making and higher service levels.
9. Underestimating Seasonal Demand
The Mistake:
Failing to scale operations during peak seasons leads to shortages, bottlenecks, and customer churn.
Avoid It By:
-
Forecasting seasonal trends using historical data.
-
Building strong relationships with flexible partners in the pallet network.
-
Keeping buffer stock and extra rack space available.
Agility is key. A responsive logistics partner ensures you meet demand even under pressure.
10. Choosing the Wrong Pallet Distribution Partner
The Mistake:
Price-driven decisions can compromise reliability, coverage, and customer service.
Avoid It By:
-
Evaluating providers based on experience, reviews, and network affiliation (e.g., Palletline UK).
-
Reviewing KPIs like delivery accuracy, damage rates, and claims handling.
-
Prioritizing a scalable partner who grows with your business.
The right pallet distribution company becomes a strategic extension of your operation—not a recurring problem.
11. Mislabeling or Poor Documentation
The Mistake:
Incorrect labels or incomplete documents delay deliveries and cause compliance issues.
Avoid It By:
-
Double-checking shipping labels and documentation before dispatch.
-
Automating documentation processes via integrated logistics software.
-
Ensuring your team is trained on international and domestic shipping requirements.
Accurate labeling reduces disputes, speeds up transit through hubs, and enhances visibility in the pallet network.
12. Not Leveraging Technology and Automation
The Mistake:
Relying solely on manual labor can limit scalability and increase human error.
Avoid It By:
-
Investing in WMS (Warehouse Management Systems) and automation solutions.
-
Using data analytics to improve routing, picking, and packing.
-
Working with logistics partners who innovate within the Palletline logistics ecosystem.
Modern tools allow you to do more with less while improving accuracy and reducing cost per unit.
Final Thoughts: Logistics Is Strategy
Pallet distribution isn’t just about moving goods—it’s about optimizing every touchpoint in your supply chain. Whether it’s selecting the right pallet size, ensuring precision in pallet racking installation, or adopting cutting-edge tracking technologies, each step offers a chance to save costs and boost customer satisfaction.
Avoiding these 12 common mistakes positions your business to:
-
Improve delivery reliability.
-
Reduce damage and return rates.
-
Maximize warehouse and transport efficiency.
-
Scale operations sustainably through a trusted pallet network.
Looking for a Logistics Partner Who Gets It Right?
At [Your Company Name], we specialize in comprehensive pallet solutions—from racking installation to nationwide delivery. As an approved member of Palletline UK, we combine the reach of a large network with the care of a local partner.
✅ Safe and secure pallet handling
✅ Seamless integration with your warehouse systems
✅ On-time deliveries across the UK
✅ Expert guidance on storage, layout, and compliance
Whether you’re shipping 10 pallets a week or 1,000, we’ve got the flexibility and infrastructure to scale with your business. Let’s eliminate inefficiencies and turn logistics into your competitive advantage.