Understanding Vacuum Pump Lubrication:Oil vs.Oil-Free System
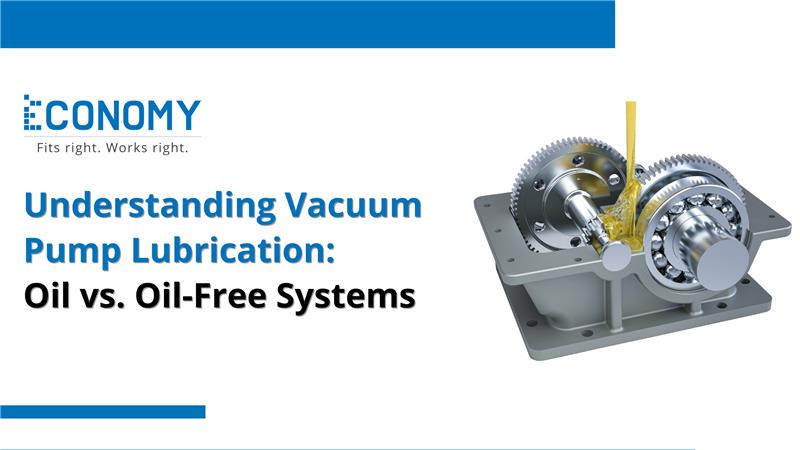
Vacuum pumps are essential components in countless industrial and scientific processes, from pharmaceutical production and food packaging to electronics manufacturing and laboratory research. One of the most important aspects of vacuum pump design and operation is lubrication, which directly affects performance, efficiency, and maintenance requirements. Depending on the application, users typically choose between oil-lubricated and oil-free vacuum pumps—two distinct technologies with unique operating principles and advantages.
Understanding the differences between these systems is critical for selecting the right vacuum pump for your needs. Oil-lubricated pumps use specialized fluids to aid in sealing, cooling, and reducing friction, while oil-free pumps rely on dry mechanisms to achieve similar results without contamination risks. In this article, we’ll explore why lubrication is essential in vacuum technology, compare oil and oil-free systems, and guide you in choosing the most suitable pump for your industry or application.
Why Do Oil-Vacuum Pumps Need Lubrication?
Oil-lubricated vacuum pumps use specially formulated oils to serve multiple functions:
-
Lubrication: The oil reduces friction between moving parts, minimizing wear and tear and extending equipment life.
-
Sealing: In rotary vane and other positive displacement pumps, oil helps create a tighter seal, improving vacuum performance.
-
Cooling: The oil absorbs and dissipates heat generated during pump operation, maintaining optimal temperature.
-
Contaminant Removal: Some vacuum oils help trap contaminants and particles, improving the purity of the vacuum environment.
Because of these properties, oil-lubricated pumps are often preferred for processes that demand high vacuum levels and extended operation.
Oil vs. Oil-Free Vacuum Pumps: Key Differences
Feature | Oil-Lubricated Pumps | Oil-Free Pumps |
---|---|---|
Lubrication | Requires vacuum oil | No oil required |
Maintenance | Regular oil changes and filter cleaning | Minimal, mostly dry maintenance |
Vacuum Level | Higher vacuum levels achievable | Moderate vacuum levels |
Contamination Risk | Potential oil carryover | No risk of oil contamination |
Cost (Initial/Operational) | Lower initial cost, higher maintenance | Higher initial cost, lower upkeep |
Applications | Industrial, chemical, and medical | Cleanrooms, electronics, packaging |
Oil-Lubricated Vacuum Pumps
How They Work
Oil-lubricated vacuum pumps—such as rotary vane, rotary piston, and diffusion pumps—use oil as a critical component in creating vacuum. In rotary vane pumps, for example, the oil helps seal the vanes and reduce friction as they rotate within the housing. These pumps can achieve vacuum levels as low as 10⁻³ mbar or better, making them ideal for high-vacuum processes.
Advantages
-
High Performance: Can reach deep vacuum levels efficiently.
-
Durability: Properly maintained pumps have long service lives.
-
Cost-Effective: Generally lower upfront costs.
Disadvantages
-
Maintenance-Intensive: Requires regular oil changes and monitoring.
-
Risk of Contamination: Oil backstreaming can contaminate the process.
-
Environmental Concerns: Disposal of used oil must be handled properly.
Oil-Free Vacuum Pumps
How They Work
Oil-free vacuum pumps (dry pumps) operate without any lubrication in the compression chamber. Instead, they use alternative mechanisms such as diaphragms, scrolls, claws, or screw rotors. These pumps are favored in applications where a contamination-free environment is critical.
Advantages
-
Clean Operation: No oil means zero risk of process contamination.
-
Low Maintenance: No oil to change; minimal service needs.
-
Eco-Friendly: No hazardous waste from used oil.
Disadvantages
-
Higher Initial Cost: More expensive upfront.
-
Lower Vacuum Capability: Usually limited to medium or rough vacuum (down to 10⁻² mbar).
-
Noise and Heat: Some dry pumps can run hotter or louder than oil-lubricated models.
Oil vs. Oil-Free Vacuum Pumps: Key Comparisons
-
Performance:
-
Oil-lubricated pumps typically outperform oil-free models in achieving deeper vacuum levels.
-
Oil-free pumps are sufficient for many medium-vacuum applications.
-
-
Cleanliness:
-
Oil-free pumps are essential for clean processes like food, pharma, or electronics.
-
Oil-lubricated pumps may require traps or filters to protect the system from oil vapors.
-
-
Maintenance:
-
Oil-lubricated pumps need consistent monitoring and servicing.
-
Oil-free pumps offer long service intervals and less downtime.
-
-
Cost:
-
While oil-free pumps have a higher purchase price, they save on maintenance and disposal costs.
-
Oil-lubricated pumps are cheaper initially but incur higher long-term operating costs.
-
How to Choose the Right Vacuum Pump for Your Industry
Selecting the right vacuum pump for your industry involves evaluating several critical factors beyond just initial cost. The required vacuum level, process cleanliness, operating environment, and maintenance capabilities should all guide your decision. For example, industries that require deep or high vacuum levels—such as metallurgy, coating, or chemical processing—often benefit from oil-lubricated pumps, which deliver powerful and consistent performance. In contrast, oil-free pumps are ideal for applications where contamination must be strictly avoided, such as in pharmaceuticals, food processing, and cleanroom manufacturing.
Additionally, consider the total cost of ownership, not just the upfront investment. Oil-lubricated pumps may be more affordable initially but come with ongoing costs for oil changes, filters, and maintenance. On the other hand, oil-free systems typically require less frequent service, reducing downtime and long-term expenses. Environmental regulations and sustainability goals are also key—oil-free pumps align better with green initiatives by eliminating hazardous waste disposal. Ultimately, matching the pump’s capabilities to your operational demands ensures efficiency, reliability, and long-term value.
Choosing between oil and oil-free systems depends on several key factors:
-
Required Vacuum Level: If your application demands deep vacuum (e.g., metallurgy, vacuum coating), go for an oil-lubricated pump.
-
Contamination Sensitivity: For cleanrooms, labs, and pharmaceutical production, oil-free is the better option.
-
Budget Constraints: Oil-lubricated pumps are less expensive upfront but consider the long-term cost of maintenance.
-
Maintenance Capabilities: If your facility can’t support frequent servicing, an oil-free pump offers convenience.
-
Environmental Regulations: Oil-free systems reduce hazardous waste and align with sustainability goals.
Conclusion
Understanding the differences between oil-lubricated and oil-free vacuum pumps is essential for making an informed investment. Each type has its strengths and trade-offs. Oil-lubricated pumps excel in high-performance, demanding environments but require regular upkeep and monitoring. Oil-free pumps are ideal for clean, sensitive operations where contamination and maintenance need to be minimized.
Ultimately, the right choice depends on your application, performance requirements, budget, and environmental goals. By weighing these factors carefully, you can select a vacuum system that delivers reliable, efficient operation with minimal compromise.